FAQ – Light ends in the heat transfer oil
Light ends in the heat transfer oil – How to act best?
This FAQ area includes some general questions and answers on and around the topic of light ends, what they are, how they are generated and how they affect the heat transfer oil in the end. Moreover, we describe the advantages of the flashpoint management and how you can avoid the formation of light ends in the best way.
What are light-ends?
Heat transfer oil is a mixture consisting of multiple components. These components distinguish by their characteristics. All components with a low boiling temperature are called light ends. The low boiling temperature also comes with a low flashpoint. In combination with oxygen, these components can most likely form an ignitable mixture and therefore, they pose the highest risk for explosion and fire.
The behaviour of light ends is like benzine and poses a safety risk in thermal oil systems.
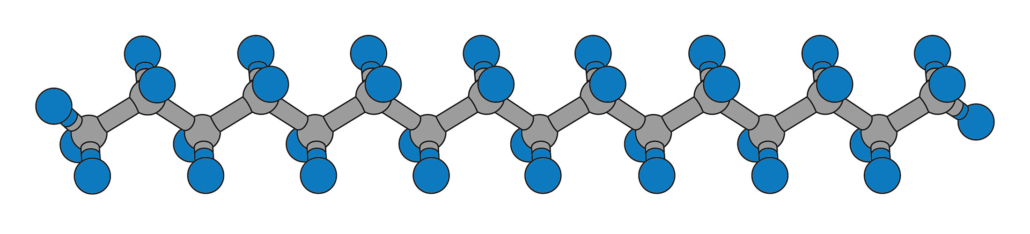
(average mass fraction in light-ends, flashpoint 71 °C)
Back to Index
How are light-ends generated and what happens in the heat transfer oil system?
Due to the high temperatures, hydrocarbons in thermal oil decompose to form hydrocarbon with shorter chains – the light-ends. This process continuously takes place in each system during operation; the quantity of the decomposition product however depends on temperature and the type of oil used.
Generally, the following items apply: The higher the operating temperature is, the higher is the generated quantity of light-ends. If the fraction of light-ends increases, the flashpoint of the heat transfer oil will be lower.
This process is completely normal. If, however, no flashpoint management has been implemented, problems will begin. Over time, the decreasing temperature of the flashpoint possibly endangers the operating safety. That means, light ends evaporate already at low temperatures and can become slightly flammable.
Furthermore, the increase of light ends supports cavitation on mechanical components of the systems, e.g. in pumps. Therefore, it is recommended to operate an active flashpoint management to keep the flashpoint on a continuously high and safe level.
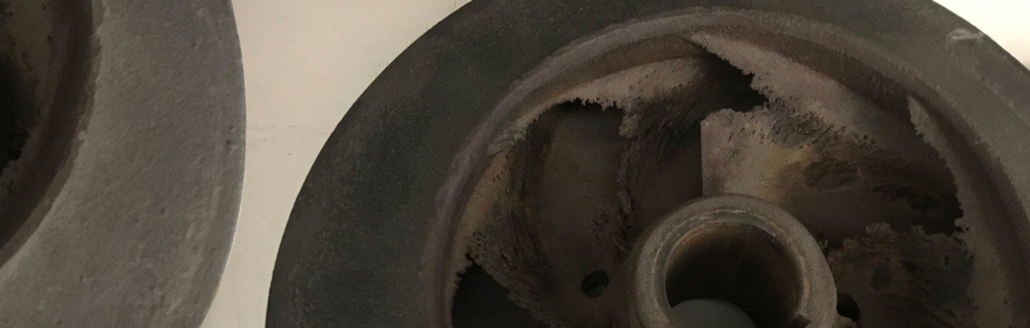
(source: Allweiler)
Back to Index
How do I determine the exact flashpoint of my oil?
It is important to know that light-ends are volatile and therefore, taking an open, hot sample of heat transfer oil provides a wrong result. Then, the sample shows a too high flashpoint and with this, a too positive result, although the flashpoint is possibly lower.
For the analysis it is most important to receive a representative and exact sample. This is ensured by a closed, cooled sampling technology.
In the NESS Sample Cooler (NPK40) the sample is cooled down by water to a temperature, at which light-ends cannot evaporate from the sample anymore. This ensures a representative analysis result.
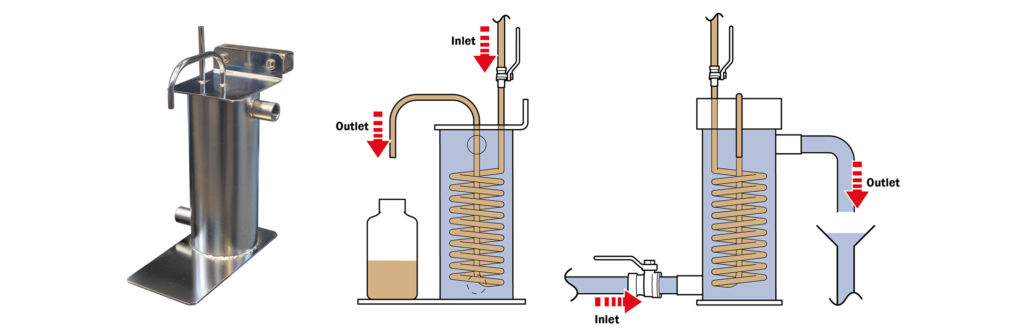
and cooled sampling technology
Back to Index
What can I do to prevent the generation of light-ends?
There are some ways to counteract the generation of light-ends.
One of the solution approaches is the partial exchange of the heat transfer oil used. In this case, part of the oil is replaced by fresh oil, whereby a certain percentage of the generated light ends will be discharged out of the system. With this, the flashpoint will increase to a higher level for a short time. However, this solution does not replace a flashpoint management and is only a short-term solution, mostly in case of an emergency. In addition, in some circumstances, the oil change is associated with a standstill of the system and – depending on the oil used – it causes high running costs.
A widely used approach approach for driving the light-ends out of the thermal oil is the so-called boiling out of the system. Even in connection with the already mentioned problem of cavitation, the heat transfer oil systems are boiled out already before the initial commissioning to drive out possibly existing water. Later, this is also done during the running operation to drive out light-ends possibly occurred. With this, it is avoided that light-ends get into the pump housing as a gas bubble and cause damages. Mostly, this process of boiling out is simply repeated in regular intervals; however, this comes again with longer standstills.
Otherwise, in addition to the methods introduced above, light ends can also be driven out of the system by means of distillation. Correctly intergraded, this solution has the advantage that it can be carried out during the running operation of the system. In this procedure the light ends are solved out of the heat transfer oil and separated. With this, the above-mentioned active flashpoint management can be implemented.
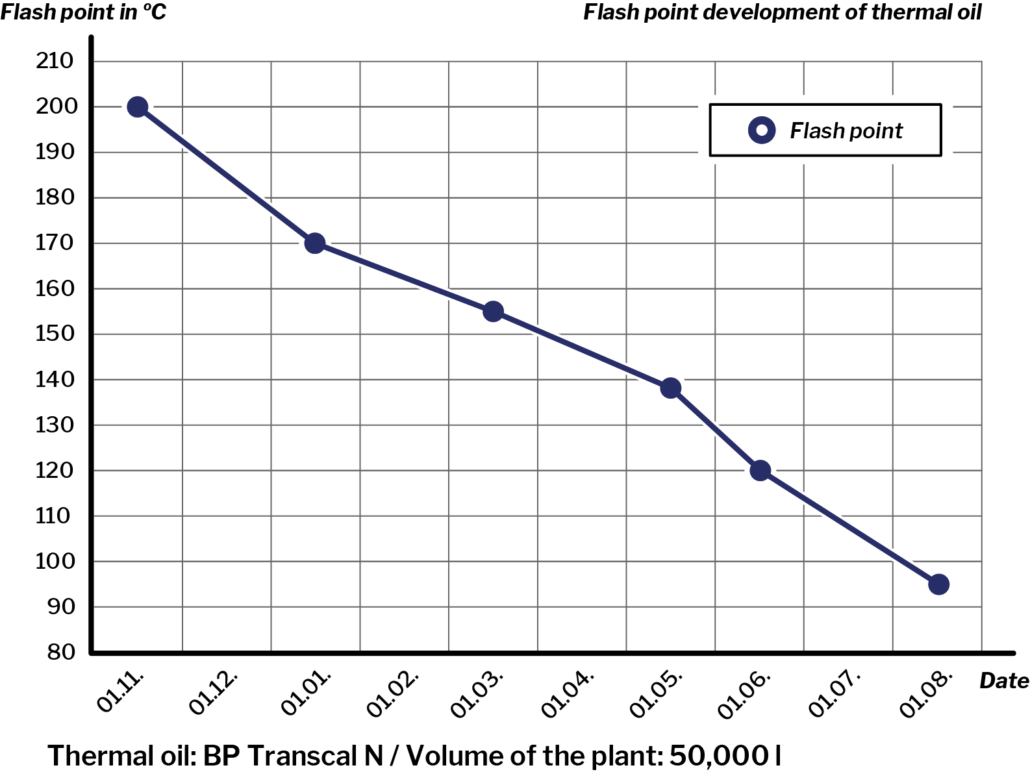
Back to Index
An active flashpoint management as preventive action against light-ends?
Exactly! Only with an active flashpoint management you will have the possibility to minimise your risks in a way that continuous oil quality is ensured referring to the flashpoint also for a long time. Here, this durably acts against fluctuations. For users of large-size systems this is a great tool for the modern risk management.
By continuous driving out of light ends the flashpoint always remains at a high, safe level. This does not only reduce the risk of fire and cavitation itself, but with this it protects the whole system and the employees sustainably. Moreover, this reduces your operational costs caused by standstills or oil change for a long term — you will have more planning safety.
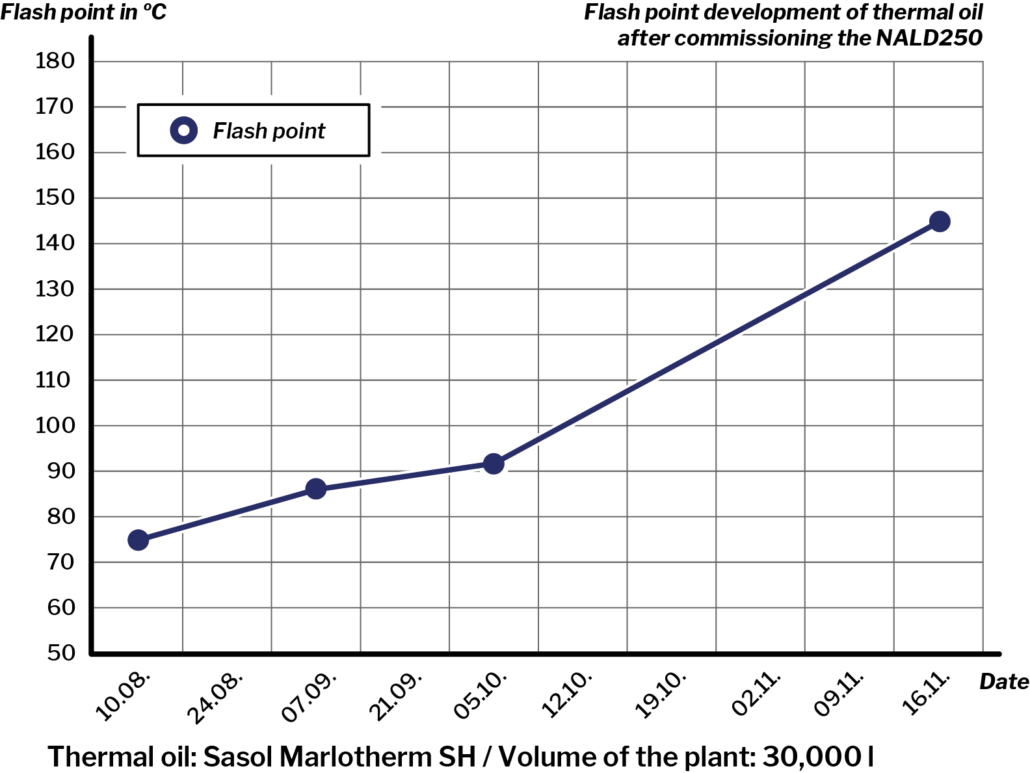
Back to Index
Other FAQ topics that might interest you
NESS NALD250 / NALD250i
Active light ends removal system NALD250 / NALD250i
for fast and flexible integration
NESS NLPA150 / NLPA250
Passive light ends removal system
NLPA150 / NLPA250 as special solution